
Project started as an ESE-383 2-bolt main, stock cap motor.
|

Snafu! This block had a blem in one of the cylinders and we
decided to set it to the side and send a different core to the
machine shop. The new block will have ProGram splayed caps.
|

While waiting for the main caps to be installed let's go ahead and get
the rest of the rotating assembly cleaned and assembled.
|

I enjoy showing off all of my work space. It helps to keep me
organized and my mind clear and fresh.
|

Mahle pistons and Callies Compstar rods.
|

Rod bearing clearance check. First install Clevite HN bearing
and torque rod bolts to 75ft-lb which should be .004 to .005"
stretch. (here it is .0048).
|

Measure crank journal then bore gauge for the differential. (.0022).
|

Here is why I need so much table top.
|

The next rod is 0.0023" bearing clearance, (using standard size
for both bearing halves).
|
Next up is to file fit
the piston rings. (I will use the original 4.030" over
block for file fitting the rings. Then more assembly as soon as
the block returns from the machine shop.
|

Top ring at 21 to 22 thousands.
|
|

Fiancée snapping a few photos.
|
|
|
|

Freshly machined splayed cap block ready for cleaning and prep.
|

Threading of oil galleries.
|

Crank test fit is nice.
|

Checking to see if rods need clearance at the block and the answer is
yes, (slight clearancing needed).
|

Block clearanced and cleaned.
|

Cam bearing installation.
|

Rear main cap oil galley plug.
|

Cam bearings.
|

Main bearing clearance. Using coated ACL bearings.
|
|

ProGram billet main caps.
|

Setting the mains a tad on the tight side.
|

Final numbers written in sharpee on the block.
|

Crank thrust is .007"
|

All rods/pistons installed and rod bolts torqued to 75ft-lb
|

Used Stef's oil pan test fit.
|

Melling oil pump #10552 requires a pickup to fit the Stef's pan.
Will work on that in the next few days.
|

Dark photo of LE camshaft.
|

Degree check at 109 intake centerline. Crank sprocket set at
"0" Cam card calls for 108 deg. Pretty close.
|

EFI Connection 1x cam reluctor.
|

The block was not "zero" decked. Only slightly
decked. Piston is in the hole .010"
|

EFI connection 24x reluctor wheel test fit.
|

Cam sensor bumps into the camshaft pin
slightly. Will remove camshaft and either hammer the pin down
further into the camshaft or grind the cam pin shorter.
|

Melling 10552 oil pump with custom pickup from Stef's.
|

Making sure that the oil pump clears the bottom of the oil pan.
I had to mash it down a bit with a persuasion tool.
|

Pulled camshaft back out and then hammered the cam pin into the cam to
make it shorter. All back together now with a short stub of a
cam pin.
|

Pistons are .010" in the hole.
|
|
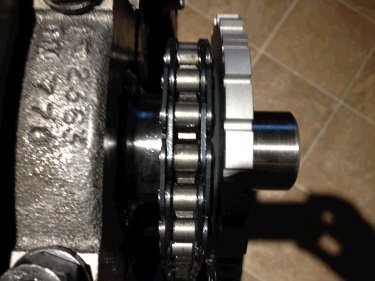
EFI connection's new reluctor. It's thicker than the 1st
generation.
|
|
|

New GM oil pump drive gear.
|
|

LE2 Heads, (Iron)
|

Mr. Gasket .026" thick head gasket.
|
|

I gave up on the Stef's pan. It was my 1st pan I owned many
years ago. I had not yet worked out all the fitment bugs.
Originally a stock oil pan was to be used on this motor and here is a
pretty good used oil pan. I will clean it up and paint it with
POR15.
|

Here is a good view of what I do to the main cap and oil dip stick
tube to allow for good oil level indication. The stick scrapes
the main cap bolt but only on one side.
|

Now the Melling oil pump has a pickup bolted on for 7.0" stock
oil pan. Here I am making sure there is oil pan clearance.
(3/8")
|

The pan fits nicely. No interference with rotating assembly.
|

Test fit of the Powerbond hub. This is for an Impala SS.
|

Pressed on.
|

Make sure the hub is all the way on and pressing onto the
reluctor. The reluctor cannot be wobbling.
|

POR15 engine paint.
|
|
|

Notice: one valve spring off. Working on valve spring change
out. Valve guide boss needs to be machined.
|
It turns out that the valve guide bosses
on the iron heads need to be machined to fit the new valve
springs. Sending heads to Brinkley Auto Machine for that job.
|

1 week later, heads are back. Let's get her buttoned up.
|

One last look at the bottom end.
|

Brand new GMPP lifters.
|

An aftermarket cam on a smaller base-circle will cause stock lifters
to dip lower into the dog-bone guide. I do not see that as a
problem as long as the lifters do not dip under the guide.
|

Lunati valve spring kit #73925K2 installed at 1.780" per Lloyd
Elliott
|

Brinkley said the guide seals provided in the kit do not fit the
valves. These are aftermarket smaller diameter stem
valves. Brinkley found and installed the smaller seals.
|

Notice a common occurrence with the Comp Pro-Magnum rockers...cosmetic
rust.
|

Oil pressure test to look for leaks and test the lifters.
|

2500rpm drill gives 58psig
|

Trick Flow pushrods, 5/16" O.D., 7.200" long
|

7.2" pushrod puts the rocker tip right in the center of the valve
tip.
|
|

Cleaned out the internal passages of the intake manifold then
installed oil splash tray, (not shown)
|

Just prior to installing intake manifold.
|

All boxed up and ready for truck shipping pick-up.
|
|
|
|
|
|